Cutting Besi | Revolusi Presisi dan Efisiensi di Pabrik Otomotif
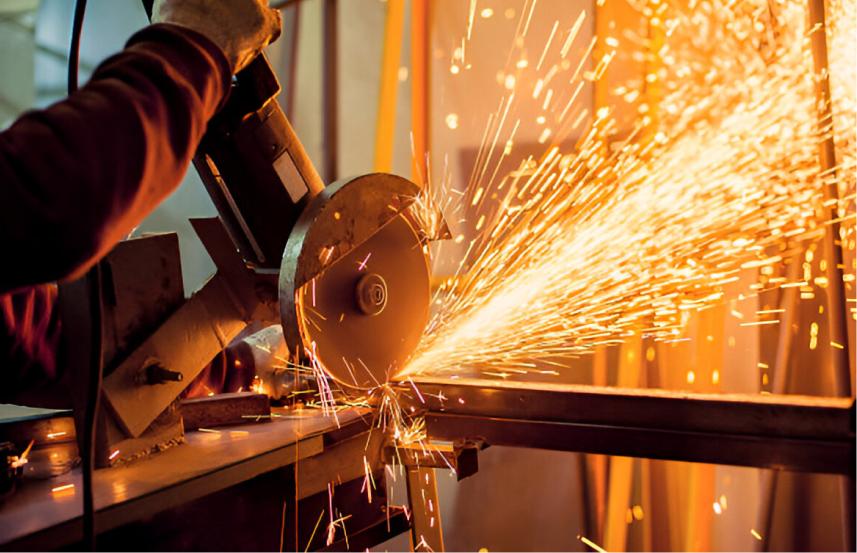
Industri otomotif global, termasuk di Indonesia, dikenal dengan tingkat persaingannya yang sangat ketat. Inovasi berkelanjutan, efisiensi lini produksi, dan kualitas komponen yang superior menjadi pilar utama bagi para pemain di industri ini untuk tetap relevan dan unggul. Setiap elemen kendaraan, mulai dari struktur rangka yang kokoh hingga detail estetika terkecil pada panel bodi, menuntut tingkat presisi yang luar biasa. Dalam konteks inilah, proses cutting besi memegang peranan fundamental dalam mewujudkan desain kendaraan modern yang tidak hanya aman dan ringan, tetapi juga menawarkan performa tinggi. Tanpa adanya teknik cutting besi yang akurat dan efisien, upaya untuk melakukan produksi massal komponen otomotif dengan standar kualitas tinggi akan menjadi sebuah tantangan besar, bahkan mustahil.
Pabrik-pabrik otomotif secara konstan dihadapkan pada berbagai tantangan, terutama dalam hal pemotongan beragam jenis material besi dan baja. Ini termasuk material-material baru yang inovatif seperti Advanced High-Strength Steels (AHSS), yang menawarkan kekuatan superior dengan bobot lebih ringan. Tuntutan untuk melakukan pemotongan dengan kecepatan tinggi, presisi maksimal, dan biaya yang minimal terus meningkat. Pertanyaan krusial yang sering muncul adalah: bagaimana pabrikan otomotif dapat memilih teknologi cutting yang paling tepat untuk kebutuhan spesifik mereka, sekaligus memastikan pasokan material baku yang konsisten dan andal?
Artikel ini akan mengupas tuntas berbagai aspek penerapan layanan cutting besi dalam lingkungan pabrik otomotif. Kita akan menjelajahi spektrum teknologi cutting besi terkini, mulai dari yang paling canggih hingga metode konvensional yang masih relevan. Lebih lanjut, akan dibahas aplikasi spesifik dari teknologi-teknologi ini dalam pembuatan komponen-komponen krusial kendaraan, serta tantangan yang kerap dihadapi, khususnya ketika berhadapan dengan material modern seperti AHSS. Selain itu, artikel ini akan menyoroti bagaimana sinergi strategis dengan distributor besi dan baja dapat menjadi solusi integral dalam rantai pasok. Pembaca diharapkan akan memperoleh pemahaman yang komprehensif dan mendalam, yang dapat menjadi landasan untuk mengoptimalkan proses fabrikasi logam di sektor otomotif yang dinamis. Pemahaman ini tidak hanya terbatas pada aspek teknis pemotongan, tetapi juga bagaimana proses ini secara langsung memengaruhi hasil akhir yang menjadi tolok ukur keberhasilan industri otomotif: keamanan kendaraan, efisiensi bobot, performa keseluruhan, dan tentu saja, efisiensi biaya produksi.
Memahami Esensi Cutting Besi dalam Industri Otomotif: Fondasi Presisi Manufaktur
Apa Itu Cutting Besi dan Mengapa Begitu Vital bagi Pabrik Mobil?
Cutting besi merupakan salah satu proses fabrikasi logam yang paling fundamental, merujuk pada serangkaian teknik yang digunakan untuk memisahkan, memotong, atau membentuk material logam, khususnya besi dan baja, agar sesuai dengan desain dan spesifikasi yang telah ditentukan. Dalam konteks industri otomotif yang sangat bergantung pada komponen logam presisi, peran cutting besi menjadi sangat vital. Proses ini bukan sekadar tindakan memotong material, melainkan sebuah langkah awal yang menentukan kualitas, keamanan, dan efisiensi produk akhir.
Vitalitas cutting besi bagi pabrik mobil dapat dilihat dari beberapa aspek krusial:
- Akurasi Dimensi: Pemotongan yang presisi memastikan bahwa setiap komponen memiliki dimensi yang sesuai dengan spesifikasi desain. Hal ini sangat penting untuk kelancaran proses perakitan, mengurangi potensi rework (pengerjaan ulang), dan mencegah kegagalan komponen akibat ketidaksesuaian ukuran. Komponen yang pas dengan sempurna akan menghasilkan kendaraan yang lebih solid dan andal.
- Efisiensi Material: Dalam produksi massal seperti di industri otomotif, setiap gram material berharga. Cutting besi yang optimal, dengan perencanaan pola potong yang cerdas, dapat meminimalkan limbah material (scrap). Ini tidak hanya berdampak pada pengurangan biaya produksi tetapi juga mendukung praktik manufaktur yang lebih berkelanjutan.
- Kualitas Komponen: Kualitas hasil potongan, seperti kehalusan tepi, ketiadaan gerinda (burr), dan minimnya deformasi atau zona terdampak panas (HAZ), secara langsung memengaruhi integritas struktural dan performa komponen tersebut. Tepi potongan yang buruk dapat menjadi titik awal retak atau korosi.
- Kecepatan Produksi: Metode cutting besi yang efisien dan cepat sangat mendukung throughput tinggi yang menjadi tuntutan dalam lini produksi otomotif. Kemampuan untuk memotong komponen dengan cepat tanpa mengorbankan kualitas adalah kunci untuk memenuhi target produksi.
Pentingnya cutting besi tidak hanya terletak pada tindakan fisiknya, tetapi lebih jauh lagi, pada bagaimana kualitas dan efisiensi proses pemotongan ini merambat dan memberikan dampak signifikan pada keseluruhan rantai nilai produksi otomotif. Mulai dari tahap desain awal, di mana batasan dan kemampuan teknologi cutting harus dipertimbangkan, hingga performa akhir kendaraan di tangan konsumen, serta aspek biaya yang kompetitif. Proses ini adalah fondasi yang menentukan apakah sebuah komponen dapat diproduksi sesuai standar, apakah kendaraan akan aman dan berfungsi dengan baik, dan apakah pabrikan dapat mencapai target efisiensi biayanya.
Evolusi Teknologi Cutting Besi: Dari Gergaji Manual hingga Robotika Canggih di Era 2025
Perjalanan teknologi cutting besi telah mengalami evolusi yang luar biasa, seiring dengan meningkatnya kompleksitas desain kendaraan dan tuntutan efisiensi produksi. Pada awalnya, proses pemotongan logam sangat bergantung pada metode manual. Penggunaan alat seperti gergaji tangan dan pahat adalah hal yang umum, namun metode ini sangat memakan waktu, membutuhkan tenaga kerja intensif, dan hasilnya seringkali kurang presisi, terutama untuk kebutuhan produksi massal skala industri.
Seiring waktu, perkembangan teknologi melahirkan mesin-mesin potong mekanis. Contohnya adalah mesin shearing (gunting plat) yang mampu memotong lembaran logam secara lurus dengan lebih cepat dan konsisten dibandingkan metode manual. Mesin gergaji pita (band saw) juga mulai digunakan untuk memotong berbagai profil material. Meskipun merupakan kemajuan signifikan, metode mekanis ini masih memiliki keterbatasan dalam hal fleksibilitas bentuk potongan dan kecepatan untuk desain yang kompleks.
Revolusi sesungguhnya dalam teknologi cutting besi datang dengan munculnya metode thermal cutting, yaitu plasma cutting dan laser cutting. Plasma cutting, yang menggunakan gas terionisasi super panas, memungkinkan pemotongan logam yang tebal dengan kecepatan tinggi. Sementara itu, laser cutting, dengan sinar laser berintensitas tinggi, menawarkan presisi yang tak tertandingi, terutama untuk detail rumit dan material tipis.
Puncak dari evolusi ini adalah integrasi teknologi cutting dengan Computer Numerical Control (CNC). Mesin cutting CNC, baik itu laser, plasma, maupun machining center, mampu melakukan pemotongan secara otomatis berdasarkan program digital, menghasilkan akurasi yang sangat tinggi, repetabilitas, dan kemampuan untuk memotong desain geometris yang paling kompleks sekalipun. Ini membuka pintu bagi desain komponen otomotif yang lebih inovatif dan optimal.
Memasuki era 2025 dan seterusnya, tren teknologi cutting besi di pabrik otomotif modern terus bergerak menuju otomatisasi penuh. Ini melibatkan penggunaan robotika untuk penanganan material dan proses cutting, serta integrasi sistem cerdas berbasis Kecerdasan Buatan (AI) untuk optimasi parameter potong secara real-time, pemeliharaan prediktif, dan kontrol kualitas otomatis. Evolusi ini bukan sekadar tentang pengembangan alat yang lebih canggih, melainkan mencerminkan perubahan paradigma dalam dunia manufaktur. Proses cutting besi kini menjadi salah satu simpul krusial dalam aliran data dan otomatisasi yang lebih besar, sejalan dengan prinsip-prinsip Industri. Investasi dalam teknologi cutting modern bukan lagi pilihan, melainkan sebuah keharusan bagi pabrikan otomotif untuk mempertahankan daya saing di pasar global.
Ragam Teknologi Cutting Besi Presisi untuk Komponen Otomotif: Memilih Alat yang Tepat
Pemilihan teknologi cutting besi yang tepat adalah keputusan krusial bagi pabrik otomotif. Setiap metode memiliki karakteristik, kelebihan, dan kekurangan yang membuatnya lebih sesuai untuk aplikasi tertentu, jenis material, dan skala produksi. Berikut adalah pembahasan mendalam mengenai ragam teknologi cutting presisi yang umum digunakan:
Laser Cutting: Presisi Tertinggi untuk Detail Intrikat Komponen Otomotif
Laser cutting adalah teknologi pemotongan yang menggunakan sinar laser berdaya tinggi, yang difokuskan pada area kecil material, untuk melelehkan, membakar, menguapkan, atau meniup material tersebut dengan bantuan gas, menghasilkan potongan yang sangat presisi. Proses ini dikendalikan secara numerik (CNC) untuk akurasi maksimal.
Jenis Laser yang Umum Digunakan:
- Fiber Laser: Sangat efisien untuk memotong berbagai jenis logam, termasuk baja, stainless steel, dan aluminium, terutama untuk material dengan ketebalan tipis hingga sedang. Fiber laser dikenal karena kecepatan potongnya yang tinggi, biaya operasional yang relatif lebih rendah untuk aplikasi tertentu, dan kualitas sinar yang baik.
- CO2 Laser: Meskipun juga dapat memotong logam (seringkali dengan bantuan gas pendorong seperti oksigen), CO2 laser juga sangat efektif untuk material non-logam seperti akrilik, kayu, dan kain. Kualitas tepi potongan dari CO2 laser bisa sangat halus.
Kelebihan Laser Cutting untuk Industri Otomotif:
- Presisi Sangat Tinggi: Laser cutting mampu mencapai toleransi yang sangat ketat, seringkali dalam rentang +/- 0.002 inci hingga +/- 0.010 inci (sekitar +/- 0.05 mm hingga +/- 0.25 mm), tergantung pada jenis laser dan material.15 Ini sangat vital untuk komponen otomotif yang memerlukan fitting presisi dan memiliki geometri yang kompleks.
- Zona Terdampak Panas (HAZ) Minimal: Karena energi panas terfokus pada area yang sangat kecil, HAZ yang dihasilkan oleh laser cutting relatif minimal. Ini mengurangi risiko distorsi material dan perubahan sifat mekanik di sekitar area potongan, sehingga seringkali mengurangi kebutuhan akan proses post-processing.
- Tepi Potongan Bersih dan Halus: Hasil potongan laser umumnya sangat bersih dan halus, seringkali tidak memerlukan proses finishing tambahan seperti deburring atau penggerindaan.
- Fleksibilitas Material dan Desain: Laser cutting dapat digunakan untuk memotong berbagai jenis material (tergantung jenis lasernya) dan berbagai ketebalan. Kemampuannya untuk mengikuti kontur yang kompleks menjadikannya ideal untuk desain-desain inovatif.
- Ideal untuk Trimming AHSS Pasca Hot Stamping: Material Press Hardenable Steel (PHS) yang telah melalui proses hot stamping menjadi sangat keras. Laser cutting 3D menjadi metode yang sangat efektif untuk melakukan trimming (pemotongan tepi) pada komponen PHS ini.
Kekurangan/Pertimbangan Laser Cutting:
- Biaya Investasi dan Operasional: Mesin laser cutting, terutama yang berdaya tinggi atau memiliki kemampuan 3D, dapat memiliki biaya investasi awal yang signifikan. Biaya operasional juga bisa lebih tinggi dibandingkan metode lain seperti plasma cutting, terutama untuk pemotongan material tebal.
- Kecepatan Potong pada Material Tebal: Untuk material baja yang sangat tebal, kecepatan potong laser mungkin lebih lambat dibandingkan plasma cutting.
- Kebutuhan Material Bersih: Kualitas permukaan material yang akan dipotong dapat mempengaruhi hasil laser cutting. Material yang rata dan bersih umumnya direkomendasikan untuk hasil optimal.
- Tantangan pada Material Reflektif: Material dengan tingkat reflektivitas tinggi, seperti tembaga atau kuningan murni, dapat menjadi tantangan bagi beberapa jenis laser karena sinar laser dapat dipantulkan kembali dan berpotensi merusak optik mesin.
Aplikasi Laser Cutting di Pabrik Otomotif:
Teknologi ini banyak digunakan untuk pembuatan komponen bodi dengan detail rumit, panel interior dan eksterior, berbagai jenis braket kecil dengan toleransi ketat, pembuatan lubang presisi, trimming komponen PHS untuk safety cage, dan pembuatan prototipe cepat. Parameter pemotongan seperti daya laser, kecepatan, dan jenis gas pendukung (misalnya, nitrogen untuk potongan bersih pada stainless steel atau oksigen untuk baja karbon) harus dioptimalkan berdasarkan jenis dan ketebalan material untuk mencapai hasil terbaik.
Pemanfaatan laser cutting bukan hanya sekadar tentang mencapai presisi tinggi, tetapi juga menjadi faktor pendukung utama bagi inovasi dalam desain kendaraan. Kemampuannya untuk memproses material-material canggih seperti PHS, yang sulit atau tidak mungkin diproses dengan metode konvensional, secara langsung mendukung pengembangan kendaraan yang lebih ringan, lebih aman, dan memiliki desain yang lebih aerodinamis serta estetis.
Plasma Cutting: Solusi Cepat dan Efisien untuk Material Baja Lebih Tebal
Plasma cutting adalah proses thermal cutting yang menggunakan jet gas terionisasi (plasma) dengan suhu sangat tinggi dan kecepatan tinggi untuk melelehkan dan kemudian meniup material logam yang akan dipotong. Gas plasma ini dihasilkan dengan melewatkan gas (seperti udara, nitrogen, oksigen, atau argon) melalui nosel berkecepatan tinggi sambil dialiri arus listrik dari elektroda ke permukaan benda kerja.
Jenis Plasma Cutting:
Proses plasma cutting dapat dilakukan secara manual menggunakan torch tangan, atau secara otomatis menggunakan sistem CNC (Computer Numerical Control). Sistem CNC memungkinkan pemotongan pola yang kompleks dengan akurasi dan repetabilitas yang lebih tinggi. Teknologi plasma terkini, seperti X-Definition Plasma, menawarkan kualitas potongan yang jauh lebih baik, mendekati kualitas laser untuk beberapa aplikasi, dengan tepi yang lebih halus dan HAZ yang lebih kecil dibandingkan plasma konvensional.
Kelebihan Plasma Cutting untuk Industri Otomotif:
- Kecepatan Potong Tinggi: Salah satu keunggulan utama plasma cutting adalah kecepatan potongnya yang tinggi, terutama pada material logam dengan ketebalan sedang hingga tebal. Ini sangat bermanfaat untuk meningkatkan produktivitas di lini produksi.
- Efektif untuk Berbagai Logam Konduktif: Plasma cutting dapat digunakan untuk memotong berbagai jenis logam yang bersifat konduktif listrik, termasuk baja karbon, stainless steel, aluminium, tembaga, dan kuningan.
- Biaya Efektif untuk Material Tebal: Untuk pemotongan material dengan ketebalan di atas sekitar 1/4 inci (6 mm), plasma cutting seringkali menawarkan biaya operasional dan investasi awal yang lebih rendah dibandingkan laser cutting.
- Kemampuan Memotong Material Kurang Ideal: Plasma cutting lebih toleran terhadap kondisi permukaan material. Ia dapat memotong material yang sedikit tidak rata, berkarat, atau bahkan yang memiliki lapisan cat tipis, meskipun kualitas potongan terbaik tetap dicapai pada material bersih.
Kekurangan/Pertimbangan Plasma Cutting:
- Toleransi dan Presisi: Meskipun sistem plasma CNC modern menawarkan presisi yang baik, toleransinya umumnya lebih lebar dibandingkan laser cutting. Toleransi tipikal bisa berkisar antara +/- 0.025 inci hingga +/- 0.040 inci (+/- 0.6 mm hingga +/- 1 mm), tergantung pada ketebalan material dan kualitas sistem plasma.
- Zona Terdampak Panas (HAZ) Lebih Besar: Proses plasma cutting menghasilkan input panas yang lebih besar ke material dibandingkan laser cutting, sehingga HAZ yang terbentuk cenderung lebih lebar. Ini berpotensi mempengaruhi sifat mekanik material di sekitar area potongan, terutama pada material yang sensitif terhadap panas atau material tipis.
- Kualitas Tepi Potongan: Tepi potongan hasil plasma cutting bisa lebih kasar dan seringkali memiliki dross (lelehan logam yang membeku kembali di tepi bawah potongan) atau slag, yang mungkin memerlukan proses finishing tambahan seperti penggerindaan. Namun, sistem plasma definisi tinggi modern telah banyak mengurangi masalah ini.
- Asap dan Kebisingan: Proses plasma cutting menghasilkan asap dan partikel logam yang cukup banyak, serta tingkat kebisingan yang tinggi, sehingga memerlukan sistem ventilasi yang baik dan perlindungan pendengaran bagi operator.
- Keterbatasan pada Material Sangat Tipis atau Detail Halus: Untuk material yang sangat tipis atau desain dengan detail yang sangat halus dan rumit, laser cutting umumnya memberikan hasil yang lebih superior.
Aplikasi Plasma Cutting di Pabrik Otomotif:
Plasma cutting banyak digunakan untuk memotong komponen sasis dan rangka bodi yang terbuat dari pelat baja yang lebih tebal, pelat baja struktural, berbagai jenis braket heavy-duty, dan untuk persiapan material (pemotongan awal lembaran atau pelat) sebelum proses fabrikasi lebih lanjut. Kesalahan umum dalam pengoperasian plasma cutting, seperti penggunaan consumables yang salah atau aus, perakitan torch yang tidak tepat, atau kecepatan potong yang tidak sesuai, dapat mempengaruhi kualitas potongan dan umur consumables.
Plasma cutting dapat dianggap sebagai workhorse di banyak pabrik otomotif, terutama untuk aplikasi yang membutuhkan kecepatan pada material tebal. Meskipun presisinya secara tradisional berada di bawah laser, kemajuan teknologi seperti X-Definition Plasma terus mempersempit celah kualitas, menjadikannya pilihan yang semakin kompetitif untuk berbagai aplikasi otomotif yang tidak selalu menuntut toleransi mikron, terutama ketika faktor biaya menjadi pertimbangan utama.
Metode Cutting Besi Lainnya: Waterjet dan Pemotongan Mekanis untuk Aplikasi Khusus
Selain laser dan plasma cutting yang dominan, terdapat metode cutting besi lain yang memiliki peran penting untuk aplikasi spesifik di industri otomotif, yaitu waterjet cutting dan berbagai teknik pemotongan mekanis.
Waterjet Cutting:
Metode ini menggunakan aliran air bertekanan sangat tinggi (bisa mencapai 60,000 psi atau lebih) yang disemprotkan melalui nosel kecil untuk memotong material. Seringkali, partikel abrasif (seperti garnet) dicampurkan ke dalam aliran air (abrasive waterjet cutting) untuk meningkatkan kemampuan potong pada material keras seperti logam.
- Kelebihan:
- Tidak Menghasilkan Zona Terdampak Panas (HAZ): Ini adalah proses pemotongan dingin (cold cutting process), sehingga tidak ada perubahan struktur mikro atau sifat mekanik material akibat panas. Sangat ideal untuk material yang sensitif terhadap panas.
- Kemampuan Memotong Hampir Semua Material: Waterjet dapat memotong berbagai jenis material, termasuk logam (baja, aluminium, titanium, tembaga), non-logam (kaca, batu, keramik), komposit, plastik, dan busa.
- Presisi Baik dan Tepi Halus: Dapat menghasilkan potongan dengan presisi yang baik dan tepi yang relatif halus tanpa gerinda.
- Tidak Ada Distorsi Termal atau Tegangan Sisa Akibat Panas.
- Kekurangan:
- Kecepatan Potong Relatif Lambat: Untuk material logam, terutama yang tebal, kecepatan potong waterjet umumnya lebih lambat dibandingkan laser atau plasma.
- Biaya Operasional: Konsumsi abrasif dan perawatan pompa bertekanan tinggi dapat membuat biaya operasionalnya relatif tinggi.
- Aplikasi Otomotif: Pemotongan material komposit untuk komponen bodi ringan, material interior seperti karpet atau trim, gasket presisi, komponen dari material eksotis atau sensitif panas, dan pembuatan prototipe khusus.
Pemotongan Mekanis (Shearing, Blanking, Sawing):
Metode ini melibatkan gaya mekanis untuk memisahkan material.
- Shearing/Guillotine: Proses ini menggunakan dua bilah pisau yang bergerak seperti gunting untuk memotong lembaran logam. Sangat efisien untuk menghasilkan potongan lurus pada lembaran logam dengan cepat.
- Blanking/Punching: Ini adalah proses di mana bentuk tertentu dipotong dari lembaran logam menggunakan die (cetakan bawah) dan punch (penekan atas). Blanking menghasilkan produk jadi dari bagian yang terpotong, sementara punching membuat lubang pada lembaran. Sangat efisien untuk produksi massal komponen kecil hingga medium dengan bentuk yang berulang.
- Sawing (Gergaji Pita, dll.): Menggunakan mata gergaji bergerigi untuk memotong material, biasanya dalam bentuk profil, batangan, atau untuk pemotongan awal material sebelum diproses lebih lanjut.
- Kelebihan:
- Kecepatan tinggi untuk operasi spesifik (misalnya, shearing untuk potongan lurus, blanking untuk volume tinggi).
- Biaya alat bisa lebih rendah untuk produksi volume sangat tinggi pada proses blanking.
- Tidak ada HAZ.
- Kekurangan:
- Terbatas pada bentuk potongan tertentu (shearing untuk lurus, sawing untuk profil).
- Kualitas tepi potongan mungkin memerlukan finishing tambahan (bisa ada burr atau deformasi).
- Tantangan signifikan saat memproses Advanced High-Strength Steels (AHSS). Kekuatan tinggi AHSS menyebabkan keausan alat yang sangat cepat, peningkatan gaya potong, dan risiko retak atau shear fracture pada tepi potongan.
- Aplikasi Otomotif: Pemotongan awal koil atau lembaran baja menjadi ukuran yang lebih kecil, produksi massal braket sederhana, ring, dan komponen kecil lainnya dari baja konvensional. Untuk AHSS, proses blanking dan trimming memerlukan perhatian khusus pada desain alat (misalnya, clearance yang tepat), pemilihan material alat (baja perkakas PM dengan ketahanan aus tinggi), penggunaan pelapis alat (coatings), dan lubrikasi yang optimal untuk memperpanjang umur alat dan menjaga kualitas tepi.
Meskipun teknologi thermal cutting seperti laser dan plasma mendominasi dalam hal presisi dan fleksibilitas untuk banyak aplikasi otomotif, waterjet dan metode pemotongan mekanis tetap memegang peranan penting dalam ceruk aplikasi tertentu. Waterjet menawarkan solusi unik untuk material non-tradisional atau yang sangat sensitif terhadap panas. Sementara itu, metode mekanis, terutama blanking, tetap menjadi pilihan ekonomis untuk produksi massal komponen sederhana dari baja lunak, dan dengan adaptasi serta teknologi perkakas yang canggih, penggunaannya pada AHSS juga terus dikembangkan. Keberadaan beragam teknologi ini menunjukkan bahwa pabrik otomotif seringkali memerlukan portofolio kapabilitas cutting yang beragam, baik secara internal maupun melalui kemitraan dengan penyedia jasa cutting spesialis.
Perbandingan Komprehensif Metode Cutting Besi untuk Aplikasi Otomotif
Untuk membantu para profesional di industri otomotif dalam membuat keputusan terkait teknologi cutting besi, berikut adalah perbandingan parameter kunci dari berbagai metode pemotongan, yang dirangkum dari berbagai sumber:
- Laser Cutting:
- Presisi/Toleransi Tipikal: Sangat Tinggi ($\pm$0.05 – $\pm$0.25 mm)
- Kualitas Tepi Potongan: Sangat Halus, Bersih, Minim Burr
- Luas Zona Terdampak Panas (HAZ): Minimal
- Kecepatan Potong Relatif: Cepat (tipis), Sedang (tebal)
- Ketebalan Material Ideal: Tipis – Sedang (hingga ~25mm baja)
- Jenis Material yang Cocok: Semua Logam (Fiber), Logam & Non-Logam (CO2)
- Biaya Investasi Awal: Tinggi
- Biaya Operasional Relatif: Sedang-Tinggi
- Contoh Aplikasi Komponen Otomotif Spesifik: Panel bodi detail, trimming PHS, braket presisi
- Kelebihan Utama: Presisi tertinggi, HAZ minimal, tepi bersih
- Kekurangan Utama: Biaya tinggi, lambat u/ sangat tebal
- Plasma Cutting (Hi-Def/X-Def):
- Presisi/Toleransi Tipikal: Tinggi ($\pm$0.2 – $\pm$1.0 mm)
- Kualitas Tepi Potongan: Halus-Sedang, Dross minimal (Hi-Def)
- Luas Zona Terdampak Panas (HAZ): Sedang-Kecil (Hi-Def)
- Kecepatan Potong Relatif: Sangat Cepat (tebal), Cepat (sedang)
- Ketebalan Material Ideal: Sedang – Sangat Tebal (hingga >50mm)
- Jenis Material yang Cocok: Logam Konduktif
- Biaya Investasi Awal: Sedang-Tinggi
- Biaya Operasional Relatif: Rendah-Sedang (lebih rendah dari laser u/ tebal)
- Contoh Aplikasi Komponen Otomotif Spesifik: Komponen sasis tebal, rangka, persiapan plat
- Kelebihan Utama: Kecepatan tinggi u/ tebal, biaya efektif u/ tebal
- Kekurangan Utama: Toleransi lebih lebar, HAZ lebih besar dari laser
- Waterjet Cutting (Abrasive):
- Presisi/Toleransi Tipikal: Tinggi ($\pm$0.1 – $\pm$0.5 mm)
- Kualitas Tepi Potongan: Halus, Tanpa Burr
- Luas Zona Terdampak Panas (HAZ): Tidak Ada (Proses Dingin)
- Kecepatan Potong Relatif: Lambat-Sedang
- Ketebalan Material Ideal: Semua Ketebalan (tergantung daya pompa)
- Jenis Material yang Cocok: Hampir Semua Material
- Biaya Investasi Awal: Tinggi
- Biaya Operasional Relatif: Tinggi (abrasif, maintenance)
- Contoh Aplikasi Komponen Otomotif Spesifik: Komposit, gasket, material sensitif panas
- Kelebihan Utama: Tanpa HAZ, potong semua material
- Kekurangan Utama: Kecepatan lambat, biaya operasional tinggi
- Mekanis (Blanking/Shearing):
- Presisi/Toleransi Tipikal: Sedang-Tinggi (tergantung alat & material)
- Kualitas Tepi Potongan: Burr, Deformasi Tepi (tergantung)
- Luas Zona Terdampak Panas (HAZ): Tidak Ada
- Kecepatan Potong Relatif: Sangat Cepat (untuk operasi spesifik)
- Ketebalan Material Ideal: Tipis – Sedang (tergantung kapasitas mesin)
- Jenis Material yang Cocok: Logam (lebih mudah pada daktilitas tinggi)
- Biaya Investasi Awal: Rendah-Tinggi (tergantung kompleksitas alat)
- Biaya Operasional Relatif: Rendah (untuk volume tinggi)
- Contoh Aplikasi Komponen Otomotif Spesifik: Braket sederhana, ring, pemotongan awal lembaran
- Kelebihan Utama: Kecepatan tinggi u/ volume besar, biaya rendah
- Kekurangan Utama: Kualitas tepi, terbatas bentuk, tantangan AHSS
Perbandingan ini berfungsi sebagai panduan awal. Pemilihan metode cutting besi yang paling optimal selalu memerlukan analisis mendalam terhadap kebutuhan spesifik aplikasi, volume produksi, jenis material yang digunakan, dan pertimbangan biaya total kepemilikan. Bagi para profesional di industri otomotif, pemahaman akan nuansa dari masing-masing teknologi ini adalah kunci untuk mengambil keputusan teknis dan investasi yang tepat guna, yang pada akhirnya akan berkontribusi pada kualitas produk, efisiensi produksi, dan daya saing di pasar.
Aplikasi Layanan Cutting Besi pada Berbagai Komponen Krusial di Pabrik Otomotif
Layanan cutting besi merupakan tulang punggung dalam produksi berbagai komponen krusial di pabrik otomotif. Dari struktur utama yang menjamin keamanan hingga detail kecil yang menunjang fungsionalitas, presisi dan efisiensi proses pemotongan memainkan peran sentral.
Fabrikasi Rangka (Sasis) dan Bodi Mobil: Peran Sentral Cutting Besi dalam Keamanan dan Estetika
Rangka kendaraan (chassis) dan Body-in-White (BIW) adalah fondasi dari setiap mobil, menentukan kekuatan struktural, perilaku saat tabrakan (crashworthiness), dan penampilan keseluruhan. Proses cutting besi adalah langkah awal yang esensial dalam fabrikasi kedua elemen vital ini.
- Rangka Kendaraan (Chassis & Body-in-White/BIW):Komponen-komponen struktural utama seperti longitudinal beams, cross members, pilar A, B, dan C, subframes, serta berbagai penguat (reinforcements) diproduksi dari berbagai jenis baja, termasuk Advanced High-Strength Steels (AHSS) yang semakin populer. Pemotongan presisi untuk komponen-komponen ini sangat krusial. Akurasi dimensi memastikan bahwa setiap bagian dapat dirakit dengan tepat, membentuk struktur yang kokoh dan mampu menyerap serta mendistribusikan energi benturan secara efektif untuk melindungi penumpang. Sebagai contoh, komponen Press Hardenable Steel (PHS) yang membentuk bagian penting dari safety cage seringkali melalui proses hot stamping dan kemudian di-trimming menggunakan teknologi laser cutting 3D untuk mencapai bentuk akhir yang presisi. Untuk elemen struktural yang terbuat dari pelat baja yang lebih tebal, plasma cutting dengan definisi tinggi dapat menjadi pilihan yang efisien.
- Panel Bodi (Eksterior & Interior):Panel-panel bodi seperti pintu, kap mesin, atap, fender, dan tutup bagasi juga merupakan hasil dari proses cutting besi pada lembaran plat baja atau aluminium. Di sini, presisi pemotongan tidak hanya penting untuk kekuatan tetapi juga untuk keselarasan panel (fit and finish) yang sempurna, yang secara langsung mempengaruhi estetika dan persepsi kualitas kendaraan. Celah antar panel yang tidak rata atau bentuk yang tidak sesuai dapat merusak penampilan mobil secara keseluruhan. Laser cutting sering digunakan untuk memotong pola-pola kompleks pada panel atau untuk material tipis yang membutuhkan tepi potongan yang sangat bersih. Sementara itu, proses blanking (pemotongan menggunakan die dan punch) efisien untuk produksi massal panel dengan bentuk standar dari lembaran baja.
Dalam konteks ini, cutting besi bukan hanya sekadar proses membentuk logam. Lebih dari itu, ia secara langsung berkontribusi pada dua aspek paling fundamental dari sebuah kendaraan: keamanan penumpang, yang dijamin oleh integritas dan kekuatan rangka, serta daya tarik visual dan kualitas persepsi, yang tercermin dari kesempurnaan dan keselarasan panel bodi. Investasi pada teknologi cutting yang tepat dan penguasaan prosesnya menjadi sangat penting untuk mencapai kedua aspek tersebut secara optimal.
Produksi Komponen Mesin dan Transmisi dengan Akurasi Cutting Besi Tingkat Tinggi
Komponen-komponen dalam sistem mesin dan transmisi adalah jantung dari sebuah kendaraan. Bagian-bagian seperti blok mesin, kepala silinder, roda gigi, poros, dan berbagai braket pendukung mesin memerlukan toleransi dimensi yang sangat ketat karena mereka adalah bagian yang bergerak, saling berinteraksi, dan beroperasi di bawah tekanan serta suhu tinggi.
Proses cutting besi untuk komponen-komponen ini menuntut tingkat akurasi tertinggi. Metode seperti CNC machining (termasuk penggilingan dan pengeboran presisi setelah pemotongan awal), laser cutting, dan terkadang waterjet cutting digunakan untuk mencapai presisi geometris dan kualitas permukaan yang dibutuhkan. Material yang digunakan seringkali adalah baja paduan khusus, besi cor, atau aluminium cor yang memiliki sifat mekanik tertentu dan memerlukan teknik serta parameter cutting yang spesifik untuk menghindari kerusakan material atau keausan alat yang berlebihan.
Kegagalan akibat pemotongan yang tidak presisi pada komponen powertrain dapat berakibat fatal pada kinerja, efisiensi bahan bakar, emisi, dan keandalan kendaraan secara keseluruhan. Celah yang terlalu besar, permukaan yang tidak rata, atau lubang yang tidak sejajar dapat menyebabkan kebocoran, getaran berlebih, keausan prematur, atau bahkan kegagalan katastrofik. Oleh karena itu, dalam produksi komponen mesin dan transmisi, tidak ada ruang untuk kompromi pada kualitas dan akurasi proses cutting besi. Ini adalah area di mana investasi dalam teknologi cutting paling canggih dan kontrol proses yang ketat memberikan pengembalian yang signifikan dalam hal kualitas dan keandalan produk.
Cutting Besi untuk Sistem Suspensi, Knalpot, dan Komponen Struktural Lainnya yang Andal
Selain rangka, bodi, mesin, dan transmisi, terdapat banyak komponen struktural dan fungsional lain dalam kendaraan yang produksinya bergantung pada proses cutting besi yang akurat dan efisien.
- Sistem Suspensi: Komponen-komponen sistem suspensi seperti lengan suspensi (control arms), knuckles, berbagai braket, dan elemen struktural lainnya yang menahan beban dinamis kendaraan dan guncangan dari jalan, diproduksi melalui pemotongan berbagai jenis baja. Komponen ini harus memiliki kekuatan, ketahanan terhadap kelelahan (fatigue resistance), dan dimensi yang presisi untuk memastikan geometri suspensi yang benar, yang berpengaruh pada kenyamanan berkendara dan stabilitas pengendalian. Kualitas tepi potongan menjadi penting untuk menghindari konsentrasi tegangan yang dapat memicu retak lelah.
- Sistem Knalpot: Sistem knalpot, yang berfungsi menyalurkan gas buang, meredam suara, dan mengontrol emisi, terdiri dari berbagai pipa dan rumah (housing) yang dibentuk dari material tahan panas seperti stainless steel atau baja aluminized. Proses cutting besi (atau baja tahan karat) digunakan untuk memotong pipa sesuai panjang dan sudut yang dibutuhkan, serta memotong plat untuk komponen seperti manifold, rumah catalytic converter, dan muffler. Laser cutting dan plasma cutting adalah metode yang umum digunakan di sini, tergantung pada ketebalan material dan kompleksitas potongan.
- Komponen Struktural Lainnya: Terdapat berbagai macam braket, penguat (reinforcements), dan cross-members berukuran lebih kecil yang tersebar di seluruh struktur kendaraan untuk menopang berbagai sistem lain atau menambah kekakuan lokal. Meskipun ukurannya mungkin kecil, presisi pemotongan tetap penting untuk kemudahan perakitan dan fungsionalitas yang benar.
Keandalan jangka panjang dari semua komponen ini sangat bergantung pada kualitas awal fabrikasi, termasuk proses cutting besi. Cacat kecil yang timbul akibat proses cutting yang kurang optimal, seperti mikro-retak, tepi yang kasar, atau HAZ yang berlebihan, dapat menjadi titik awal kegagalan komponen di kemudian hari akibat getaran konstan, beban siklik, atau paparan lingkungan korosif. Oleh karena itu, pemilihan metode cutting yang sesuai dan kontrol kualitas yang ketat adalah esensial untuk memastikan setiap komponen, besar maupun kecil, memenuhi standar daya tahan dan keandalan yang diharapkan dari sebuah kendaraan modern.
Era Material Baru: Tantangan dan Solusi Cutting Besi untuk Advanced High-Strength Steels (AHSS) di Otomotif
Industri otomotif terus berinovasi dalam penggunaan material untuk mencapai tujuan ganda: meningkatkan keselamatan penumpang dan mengurangi bobot kendaraan demi efisiensi bahan bakar dan pengurangan emisi. Salah satu terobosan material yang paling signifikan adalah pengembangan dan adopsi Advanced High-Strength Steels (AHSS). Namun, keunggulan yang ditawarkan AHSS juga datang dengan tantangan baru dalam proses manufaktur, terutama dalam hal cutting besi.
Mengenal Advanced High-Strength Steels (AHSS): Material Pilihan untuk Mobil Lebih Ringan dan Aman
Advanced High-Strength Steels (AHSS) adalah kelompok baja canggih yang dirancang untuk memiliki kekuatan tarik (tensile strength) yang jauh lebih tinggi dibandingkan baja konvensional. Kekuatan superior ini memungkinkan para insinyur otomotif untuk menggunakan lembaran baja yang lebih tipis dalam desain komponen tanpa mengorbankan, bahkan seringkali meningkatkan, kekuatan dan kekakuan struktural. Hasilnya adalah pengurangan bobot kendaraan (lightweighting) yang signifikan, yang berkontribusi langsung pada peningkatan efisiensi bahan bakar dan pengurangan emisi CO2. Selain itu, AHSS memainkan peran krusial dalam meningkatkan keselamatan penumpang karena kemampuannya yang lebih baik dalam menyerap energi benturan saat terjadi tabrakan.
Jenis-jenis Utama AHSS dan Karakteristiknya untuk Aplikasi Otomotif:
- Dual Phase (DP) Steels: Baja DP memiliki struktur mikro yang terdiri dari fasa ferit yang lunak dan ulet, serta fasa martensit yang keras dan kuat. Kombinasi ini memberikan keseimbangan yang baik antara kekuatan dan kemampuan bentuk (formability). Baja DP banyak digunakan untuk komponen struktural seperti pilar, reinforcements, dan bagian-bagian yang memerlukan penyerapan energi.
- Transformation-Induced Plasticity (TRIP) Steels: Baja TRIP mengandung sejumlah fasa austenit sisa (retained austenite) dalam struktur mikronya. Selama proses deformasi (pembentukan), austenit sisa ini akan bertransformasi menjadi martensit yang sangat keras, sehingga meningkatkan kekuatan dan daktilitas material secara signifikan. Ini membuat baja TRIP cocok untuk komponen dengan bentuk yang kompleks dan memerlukan kemampuan penyerapan energi yang tinggi, seperti crash boxes dan side impact beams.
- Martensitic (MS) Steels: Baja Martensitik memiliki kekuatan yang sangat tinggi, seringkali melebihi 1200 MPa, namun dengan formability yang lebih rendah dibandingkan DP atau TRIP. Baja MS ideal untuk komponen anti-intrusi yang memerlukan kekuatan maksimum untuk melindungi penumpang, seperti bumper beams dan door intrusion beams.
- Press Hardenable Steels (PHS) / Boron Steels: Juga dikenal sebagai baja hot stamping, PHS adalah jenis baja yang dibentuk pada suhu tinggi (proses austenitisasi) dan kemudian didinginkan dengan sangat cepat di dalam cetakan (die quenching) untuk mencapai struktur martensitik penuh dan kekuatan ultra-tinggi, bisa mencapai 1500 MPa atau lebih. PHS sangat ideal untuk komponen-komponen kritis dalam safety cage kendaraan, seperti pilar A dan B, roof rails, rocker panels, dan bumper beams, karena kemampuannya membentuk geometri kompleks dengan kekuatan sangat tinggi.
- Jenis lain seperti Complex Phase (CP) steels dan Ferrite-Bainite (FB) steels juga termasuk dalam keluarga AHSS, masing-masing dengan kombinasi sifat mekanik yang unik untuk aplikasi tertentu.
Penggunaan AHSS dalam industri otomotif bukan lagi sekadar tren, melainkan telah menjadi kebutuhan fundamental. Tuntutan regulasi keselamatan yang semakin ketat di seluruh dunia, ditambah dengan target efisiensi bahan bakar dan pengurangan emisi yang ambisius, mendorong para produsen mobil untuk terus meningkatkan persentase penggunaan AHSS dalam desain kendaraan mereka. Kemampuan AHSS untuk memberikan solusi yang lebih ringan namun lebih kuat menjadikannya material kunci dalam mencapai tujuan-tujuan desain kendaraan modern.
Tantangan Spesifik Pemotongan AHSS: Lebih dari Sekadar Baja Biasa
Meskipun menawarkan banyak keuntungan, sifat unik dari Advanced High-Strength Steels (AHSS) menghadirkan serangkaian tantangan spesifik dalam proses cutting besi, yang berbeda secara signifikan dari pemotongan baja konvensional.
- Peningkatan Kekuatan dan Kekerasan: Sifat utama AHSS, yaitu kekuatannya yang tinggi, secara langsung menyebabkan keausan alat (tool wear) yang jauh lebih cepat dan parah pada metode pemotongan mekanis seperti blanking, shearing, dan punching. Alat potong akan lebih cepat tumpul, memerlukan penggantian lebih sering, dan meningkatkan biaya perkakas. Fenomena abrasive wear, di mana partikel keras dalam AHSS menggores permukaan alat, menjadi sangat dominan.
- Formabilitas Rendah dan Risiko Retak/Patah Tepi (Edge Fracture / Shear Fracture): AHSS, terutama grade dengan kekuatan sangat tinggi, cenderung memiliki daktilitas dan formability yang lebih rendah. Hal ini membuat mereka lebih rentan terhadap pembentukan retak atau patahan pada tepi hasil potongan, terutama selama proses pembentukan (forming) selanjutnya jika kualitas tepi potongan awal buruk. Fenomena shear fracture, di mana retakan terjadi pada radius kecil dengan regangan rendah, adalah masalah umum. Oleh karena itu, kualitas tepi hasil cutting besi menjadi parameter yang sangat krusial untuk AHSS.
- Sensitivitas Zona Terdampak Panas (HAZ): Beberapa jenis AHSS, dengan struktur mikro yang kompleks, bisa sangat sensitif terhadap input panas yang dihasilkan selama proses thermal cutting seperti laser dan plasma. Panas ini dapat mengubah sifat mekanik material di Zona Terdampak Panas (HAZ), seperti penurunan kekuatan atau peningkatan kerapuhan, yang pada akhirnya dapat mempengaruhi performa komponen jadi. Pengendalian HAZ menjadi sangat penting.
- Springback Tinggi: Meskipun lebih merupakan tantangan dalam proses forming, springback (kembalinya material ke bentuk semula setelah gaya pembentukan dihilangkan) pada AHSS sangat signifikan. Persiapan blank (potongan awal) dengan akurasi dimensi yang tinggi melalui proses cutting yang presisi menjadi penting untuk membantu mengelola dan mengkompensasi springback.
- Galling (Adhesive Wear): Terutama pada AHSS yang memiliki lapisan pelindung (coated AHSS) atau pada jenis stainless AHSS, material cenderung menempel (stick) pada permukaan alat potong selama proses mekanis. Fenomena ini dikenal sebagai galling atau adhesive wear, yang dapat merusak permukaan alat dan benda kerja, serta meningkatkan gaya potong.
- Trimming PHS setelah Hot Stamping: Material Press Hardenable Steel (PHS) setelah melalui proses hot stamping mencapai kekerasan yang sangat tinggi. Hal ini membuat proses trimming (pemotongan tepi untuk mendapatkan bentuk akhir) menggunakan metode mekanis konvensional menjadi hampir tidak mungkin atau sangat tidak efisien karena keausan alat yang ekstrem. Oleh karena itu, laser cutting 3D seringkali menjadi solusi utama dan paling efektif untuk trimming komponen PHS.
Tantangan-tantangan dalam cutting besi AHSS ini tidak hanya bersifat teknis operasional semata. Mereka memiliki implikasi yang lebih luas terhadap biaya produksi (karena penggantian alat yang lebih sering, potensi rework, dan siklus waktu yang lebih lama), kualitas produk akhir (dengan adanya risiko kegagalan komponen akibat kualitas potongan yang buruk), dan kecepatan produksi secara keseluruhan. Mengatasi tantangan ini memerlukan pemahaman mendalam tentang perilaku material AHSS, pemilihan teknologi cutting yang tepat, serta pendekatan yang lebih ilmiah dan kolaboratif dalam menentukan parameter proses dan strategi perkakasan.
Solusi dan Praktik Terbaik untuk Cutting AHSS: Menaklukkan Material Canggih di Tahun 2025
Menghadapi tantangan dalam cutting besi untuk Advanced High-Strength Steels (AHSS) memerlukan pendekatan yang komprehensif dan penerapan praktik terbaik. Berikut adalah beberapa solusi dan strategi kunci yang dapat diadopsi oleh pabrik otomotif dan penyedia jasa cutting untuk menaklukkan material canggih ini di tahun 2025 dan seterusnya:
1. Pemilihan Teknologi Cutting yang Tepat:
- Laser Cutting: Seringkali menjadi pilihan utama untuk AHSS karena presisinya yang tinggi, HAZ yang minimal, dan kemampuan menghasilkan tepi potongan berkualitas tinggi. Ini sangat krusial untuk trimming komponen PHS setelah hot stamping, memotong detail kompleks, dan aplikasi di mana integritas tepi sangat penting untuk proses forming selanjutnya atau untuk performa kelelahan (fatigue life). Parameter laser seperti daya, kecepatan potong, jenis dan tekanan gas pendukung (misalnya, nitrogen sering digunakan untuk potongan bersih pada AHSS untuk menghindari oksidasi) harus dioptimalkan secara cermat berdasarkan jenis dan ketebalan AHSS.
- Plasma Cutting (Advanced): Sistem plasma definisi tinggi (seperti X-Definition Plasma) dapat menjadi alternatif yang lebih ekonomis dibandingkan laser untuk pemotongan AHSS dengan ketebalan tertentu. Teknologi ini menawarkan kualitas potongan yang jauh lebih baik dibandingkan plasma konvensional, dengan taper (kemiringan tepi) yang lebih kecil dan permukaan yang lebih halus. Namun, HAZ yang dihasilkan umumnya masih lebih besar daripada laser, sehingga perlu dipertimbangkan dampaknya terhadap sifat material.
- Waterjet Cutting: Karena merupakan proses pemotongan dingin, waterjet (terutama dengan abrasif) ideal jika HAZ harus dihindari sama sekali. Metode ini dapat memotong hampir semua jenis AHSS tanpa mengubah struktur mikronya. Namun, kecepatan potongnya mungkin lebih lambat dibandingkan laser atau plasma untuk aplikasi volume tinggi.
- Pemotongan Mekanis (Blanking/Trimming Dingin):
- Untuk AHSS yang akan melalui proses cold forming, pemotongan mekanis masih dapat digunakan, tetapi memerlukan tooling yang sangat kuat, kaku, dan tahan aus. Material alat perkakas berbasis powder metallurgy (PM) seperti Vanadis atau Vancron, yang memiliki kombinasi kekerasan, ketangguhan, dan ketahanan aus yang superior, sering direkomendasikan.
- Desain alat yang cermat, termasuk clearance (celah antara punch dan die) yang optimal, sudut potong yang tepat, dan geometri alat yang dirancang untuk mengurangi konsentrasi tegangan, sangat penting.
- Penggunaan pelapis (coatings) PVD (Physical Vapor Deposition) pada permukaan alat dapat secara signifikan mengurangi gesekan, mencegah galling, dan meningkatkan umur alat.
- Lubrikasi yang efektif, menggunakan pelumas dengan aditif Extreme Pressure (EP) atau High Solids Polymer (HSP), krusial untuk mengurangi gesekan dan panas selama proses pemotongan mekanis AHSS.
- Untuk PHS yang sudah dikeraskan, pemotongan mekanis umumnya tidak direkomendasikan kecuali jika area yang akan dipotong telah melalui proses pelunakan lokal terlebih dahulu (misalnya, melalui pemanasan laser terkontrol).
2. Optimalisasi Parameter Proses:
Ini adalah kunci untuk semua metode cutting, terutama untuk laser dan plasma. Parameter seperti daya, kecepatan, frekuensi (untuk laser pulsa), jenis dan tekanan gas pendukung, serta posisi fokus harus disesuaikan dengan cermat untuk setiap jenis dan ketebalan AHSS guna mengontrol lebar HAZ, kualitas tepi potongan (minim dross, burr, dan kekasaran), dan memaksimalkan kecepatan produksi.
3. Manajemen Kualitas Tepi:
Kualitas tepi potongan AHSS memiliki dampak signifikan pada formability selanjutnya dan performa kelelahan komponen. Inspeksi tepi potong secara reguler, baik visual maupun menggunakan metode pengukuran yang lebih canggih, sangat penting. Jika diperlukan, proses post-processing seperti deburring ringan atau polishing dapat dilakukan untuk menghilangkan cacat kecil dan meningkatkan kualitas tepi, terutama untuk komponen-komponen kritis yang akan mengalami regangan tinggi atau beban siklik.
4. Kolaborasi dengan Pemasok Baja dan Ahli Cutting:
Setiap grade AHSS memiliki karakteristik unik. Bekerja sama secara erat dengan pemasok baja untuk memahami sifat spesifik material yang digunakan (seperti kurva aliran, batas formability, sensitivitas HAZ) dan berkonsultasi dengan ahli teknologi cutting dapat membantu dalam menentukan parameter proses yang paling optimal dan strategi perkakasan yang efektif.
Mengatasi tantangan cutting besi AHSS memerlukan pendekatan holistik yang tidak hanya fokus pada satu aspek. Ini adalah sebuah “rekayasa proses pemotongan” yang menggabungkan pemilihan teknologi yang tepat, penggunaan material alat yang superior, optimasi parameter proses yang cermat, dan manajemen kualitas tepi yang proaktif. Dengan strategi yang tepat, pabrikan otomotif dapat memanfaatkan sepenuhnya potensi material AHSS untuk menciptakan kendaraan yang lebih ringan, lebih aman, dan lebih efisien.
Panduan Cutting untuk Jenis-Jenis AHSS Utama di Industri Otomotif
Memilih metode dan parameter cutting besi yang optimal sangat bergantung pada jenis Advanced High-Strength Steel (AHSS) yang digunakan. Berikut adalah panduan ringkas untuk beberapa jenis AHSS utama yang umum diaplikasikan dalam industri otomotif, merangkum rekomendasi dan pertimbangan kunci berdasarkan berbagai sumber:
- Dual Phase (DP) Steel (misal DP800, DP980):
- Metode Cutting Utama yang Direkomendasikan: Laser Cutting, Plasma Cutting (Hi-Def), Mekanis (dengan tooling khusus)
- Pertimbangan Kualitas Tepi: Kritis-Sedang
- Potensi Masalah Utama Saat Cutting: Tool Wear (mekanis), HAZ (termal), Edge Cracking (jika tepi buruk)
- Solusi/Praktik Terbaik Kunci: Optimasi parameter laser/plasma, tool steel PM & coating (mekanis), lubrikasi, kontrol clearance
- Contoh Komponen Otomotif Tipikal: Pilar, Reinforcements, Cross members, Komponen struktural
- TRIP Steel (Transformation-Induced Plasticity):
- Metode Cutting Utama yang Direkomendasikan: Laser Cutting, Plasma Cutting (Hi-Def)
- Pertimbangan Kualitas Tepi: Kritis
- Potensi Masalah Utama Saat Cutting: HAZ (dapat mempengaruhi transformasi austenit), Edge Cracking
- Solusi/Praktik Terbaik Kunci: Kontrol input panas (laser/plasma), parameter potong presisi, kualitas tepi sangat penting untuk formability
- Contoh Komponen Otomotif Tipikal: Komponen dengan formability tinggi, Crash boxes, Struktur penyerap energi
- Martensitic (MS) Steel (misal MS1500):
- Metode Cutting Utama yang Direkomendasikan: Laser Cutting, Waterjet Cutting (abrasif)
- Pertimbangan Kualitas Tepi: Kritis
- Potensi Masalah Utama Saat Cutting: Tool Wear sangat tinggi (mekanis hampir tidak mungkin), HAZ, Micro-cracking
- Solusi/Praktik Terbaik Kunci: Laser cutting dengan parameter optimal (kecepatan, gas), hindari pemanasan berlebih
- Contoh Komponen Otomotif Tipikal: Komponen anti-intrusi, Bumper beams, Door intrusion beams
- PHS (Press Hardenable Steel) (misal 22MnB5 setelah hot stamping):
- Metode Cutting Utama yang Direkomendasikan: 3D Laser Cutting (utama untuk trimming), Waterjet (abrasif)
- Pertimbangan Kualitas Tepi: Sangat Kritis
- Potensi Masalah Utama Saat Cutting: Material sangat keras, sulit dipotong mekanis, HAZ pada PHS berlapis (misal AlSi)
- Solusi/Praktik Terbaik Kunci: Laser cutting dengan daya dan gas optimal, fixture yang baik untuk komponen 3D, pertimbangkan lapisan jika ada
- Contoh Komponen Otomotif Tipikal: Pilar A/B, Roof rails, Rocker panels, Tunnel, Komponen safety cage
Catatan Penting:
- Kualitas Tepi: “Kritis” berarti kualitas tepi sangat mempengaruhi performa pembentukan selanjutnya atau umur kelelahan komponen. “Sedang” berarti penting namun mungkin ada toleransi lebih.
- Tool Wear: Terutama relevan untuk pemotongan mekanis.
- HAZ (Heat Affected Zone): Relevan untuk laser dan plasma. Pengaruhnya bervariasi tergantung grade AHSS dan parameter proses.
- Solusi/Praktik Terbaik: Ini adalah contoh, dan parameter spesifik harus selalu divalidasi melalui uji coba.
Panduan ini bersifat umum. Dalam praktiknya, kolaborasi erat antara insinyur material, desainer produk, dan spesialis proses manufaktur (termasuk ahli cutting besi) sangat penting untuk menentukan strategi pemotongan yang paling efektif dan ekonomis untuk setiap aplikasi AHSS spesifik di industri otomotif. Pemahaman mendalam tentang interaksi antara material, proses cutting, dan persyaratan performa komponen adalah kunci sukses dalam memanfaatkan potensi penuh dari material canggih ini.
Peran Strategis Distributor Besi dan Baja dalam Rantai Pasok Cutting Otomotif: Kemitraan Menuju Efisiensi
Dalam ekosistem industri otomotif yang kompleks dan bergerak cepat, peran distributor besi dan baja telah berevolusi secara signifikan. Mereka tidak lagi hanya berfungsi sebagai pemasok material mentah, tetapi telah bertransformasi menjadi mitra strategis yang menawarkan berbagai layanan nilai tambah, termasuk layanan cutting besi presisi. Kemitraan ini menjadi semakin krusial bagi pabrik otomotif untuk mencapai efisiensi operasional dan fokus pada kompetensi inti mereka.
Lebih dari Sekadar Pemasok: Nilai Tambah Distributor Besi Baja Modern untuk Pabrik Otomotif di Tahun 2025
Peran tradisional distributor besi dan baja yang hanya menyediakan material telah bergeser. Di era modern, terutama untuk melayani industri dengan tuntutan tinggi seperti otomotif, distributor telah menjadi steel service centers yang menawarkan berbagai solusi terintegrasi.
Penyediaan Material Berkualitas dan Beragam:
Fungsi dasar ini tetap penting. Distributor modern menyediakan akses ke berbagai jenis dan grade besi serta baja, termasuk baja karbon, baja paduan, stainless steel, dan yang paling relevan untuk konteks ini, Advanced High-Strength Steels (AHSS) dengan spesifikasi otomotif yang ketat. Mereka juga memastikan bahwa material yang dipasok memenuhi standar kualitas internasional maupun nasional, seringkali disertai dengan sertifikasi material yang menjamin traceability dan komposisi kimia serta sifat mekanik yang sesuai. Lebih lanjut, untuk mendukung operasional pabrik otomotif secara keseluruhan atau proyek konstruksi terkait, distributor juga dapat menyediakan material pendukung seperti besi beton untuk pondasi dan struktur bangunan pabrik, besi hollow yang serbaguna untuk rangka pendukung, jig, atau struktur non-kritis lainnya, dan besi wiremesh untuk penguatan lantai atau aplikasi sekunder lainnya. Ketersediaan beragam produk ini dari satu sumber terpercaya seperti distibutor besi, besi beton sni, besi hollow, besi wiremesh dapat menyederhanakan proses pengadaan bagi pabrik otomotif.
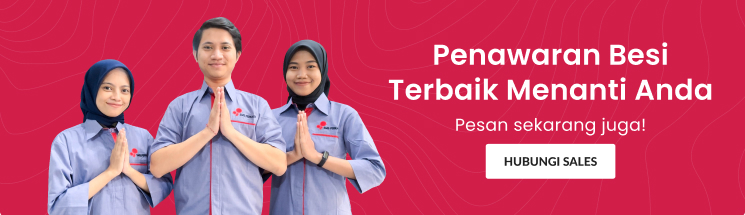
Layanan Pra-Pemrosesan (Value-Added Services):
Ini adalah area di mana distributor modern benar-benar menunjukkan nilai tambahnya:
- Jasa Cutting Presisi: Banyak steel service centers kini dilengkapi dengan fasilitas cutting besi canggih, termasuk mesin laser cutting, plasma cutting (termasuk definisi tinggi), shearing, dan slitting (pembelahan koil menjadi strip yang lebih sempit), serta cut-to-length (pemotongan koil menjadi lembaran dengan panjang tertentu) sesuai spesifikasi pelanggan. Dengan layanan ini, pabrik otomotif dapat menerima material yang sudah dipotong sesuai ukuran dan bentuk yang dibutuhkan, siap untuk proses fabrikasi selanjutnya. Ini secara signifikan mengurangi kebutuhan pabrik otomotif untuk berinvestasi dalam peralatan cutting mahal, menghemat ruang pabrik, dan mengurangi kompleksitas operasional internal.
- Blanking, Punching, dan Fabrikasi Ringan Lainnya: Beberapa distributor bahkan menawarkan layanan fabrikasi ringan lebih lanjut, seperti pembuatan blank (potongan awal) atau komponen sederhana.
Manajemen Inventaris dan Logistik:
Distributor modern seringkali menawarkan solusi manajemen inventaris yang canggih, termasuk pengiriman Just-in-Time (JIT). Ini memungkinkan pabrik otomotif untuk mengurangi biaya penyimpanan material di lokasi mereka, meminimalkan risiko kerusakan atau keusangan material, dan memastikan kelancaran aliran material ke lini produksi, sehingga mendukung prinsip-prinsip lean manufacturing.
Keahlian Teknis dan Konsultasi:
Distributor yang memiliki pemahaman mendalam tentang material dan prosesnya dapat memberikan layanan konsultasi teknis. Ini bisa berupa bantuan dalam pemilihan grade baja yang paling sesuai untuk aplikasi tertentu, rekomendasi mengenai proses cutting yang optimal, atau bahkan solusi untuk mengatasi tantangan fabrikasi yang dihadapi oleh pelanggan.
Distributor besi dan baja modern, dengan demikian, bertindak sebagai perpanjangan tangan dari fasilitas produksi pabrik otomotif. Mereka mengambil alih sebagian dari proses pra-produksi yang krusial dan padat modal, memungkinkan Original Equipment Manufacturers (OEM) otomotif untuk lebih memfokuskan sumber daya dan energi mereka pada kompetensi inti seperti desain kendaraan, perakitan akhir, kontrol kualitas, dan pemasaran. Kemitraan semacam ini adalah kunci untuk menciptakan rantai pasok yang lebih ramping, responsif, dan efisien.
Sinergi Pabrik Otomotif dengan Distributor Penyedia Layanan Cutting: Kunci Sukses Produksi Ramping
Kolaborasi antara pabrik otomotif dan distributor besi baja yang menyediakan layanan cutting besi menawarkan berbagai keuntungan strategis yang mendukung implementasi prinsip-prinsip produksi ramping (lean manufacturing) dan meningkatkan daya saing secara keseluruhan.
- Efisiensi Biaya yang Signifikan:Salah satu manfaat paling nyata adalah pengurangan biaya. Pabrik otomotif dapat menghindari investasi modal yang besar untuk pengadaan dan pemeliharaan mesin-mesin cutting canggih (laser, plasma, dll.). Selain itu, biaya tenaga kerja terampil yang dibutuhkan untuk mengoperasikan dan memelihara peralatan tersebut juga dapat ditekan. Distributor, dengan skala operasi yang melayani banyak pelanggan, dapat mengoptimalkan penggunaan material (misalnya, dengan nesting pola potong dari koil besar untuk berbagai pesanan), sehingga mengurangi limbah material dan menawarkan harga yang lebih kompetitif untuk komponen yang sudah dipotong.
- Peningkatan Fokus pada Kompetensi Inti:Dengan mengalihdayakan sebagian proses pra-pemrosesan material seperti cutting besi kepada distributor spesialis, pabrik otomotif dapat lebih memfokuskan sumber daya internal baik itu modal, manusia, maupun waktu pada aktivitas yang menjadi kompetensi inti mereka. Ini termasuk inovasi desain kendaraan, teknologi perakitan yang efisien, kontrol kualitas produk akhir yang ketat, serta strategi pemasaran dan layanan pelanggan.
- Fleksibilitas dan Skalabilitas Produksi:Permintaan pasar otomotif seringkali berfluktuasi. Dengan bermitra dengan distributor penyedia layanan cutting, pabrik otomotif mendapatkan fleksibilitas untuk menyesuaikan volume pesanan material yang sudah dipotong sesuai dengan kebutuhan produksi aktual. Mereka dapat dengan mudah meningkatkan atau menurunkan pesanan tanpa terbebani oleh kapasitas cutting internal yang mungkin tidak termanfaatkan secara optimal atau justru menjadi bottleneck.
- Akses ke Teknologi Cutting Terbaru:Distributor besi baja yang progresif dan berorientasi pada layanan akan cenderung berinvestasi pada teknologi cutting besi terkini dan tercanggih untuk memenuhi tuntutan pelanggan dan mempertahankan keunggulan kompetitif. Kemitraan dengan distributor semacam itu memberikan akses kepada pabrik otomotif terhadap teknologi tersebut tanpa mereka harus menanggung risiko dan biaya penuh dari investasi teknologi.
- Jaminan Kualitas dan Konsistensi Material:Distributor yang memiliki reputasi baik dan sistem manajemen kualitas yang solid (misalnya, sertifikasi ISO 9001 seperti yang dimiliki VAP Steel 39) dapat memberikan jaminan atas kualitas material yang dipasok dan konsistensi hasil potongan. Ini mengurangi risiko variabilitas dalam proses produksi pabrik otomotif dan membantu menjaga standar kualitas produk akhir.
Sebagai contoh, bayangkan sebuah pabrik otomotif yang meluncurkan model baru yang menggunakan komponen dari Advanced High-Strength Steel (AHSS). Daripada berinvestasi besar pada mesin laser 3D khusus untuk trimming komponen PHS dan melatih operator, pabrik tersebut dapat bermitra dengan steel service center yang sudah memiliki kapabilitas tersebut. Ini memungkinkan peluncuran produk yang lebih cepat, biaya awal yang lebih rendah, dan fokus pada perakitan model baru tersebut. Prinsip-prinsip efisiensi ini sejalan dengan praktik yang telah terbukti di industri baja global, seperti di Jepang, di mana perusahaan manufaktur besar mendelegasikan pekerjaan pemotongan dan distribusi baja kepada perusahaan sirkulasi spesialis.
Kolaborasi ini bukan sekadar hubungan transaksional jual-beli material, melainkan berkembang menjadi kemitraan strategis jangka panjang. Keberhasilan pabrik otomotif dalam menerapkan strategi produksi yang gesit (agile) dan ramping sangat bergantung pada keandalan, kapabilitas, dan responsivitas dari mitra distributor mereka, terutama yang mampu menyediakan layanan cutting besi presisi dan bernilai tambah lainnya.
Kriteria Memilih Distributor Besi Baja dan Penyedia Jasa Cutting untuk Industri Otomotif
Memilih mitra distributor besi baja dan penyedia jasa cutting besi yang tepat adalah keputusan strategis bagi pabrik otomotif. Pilihan ini akan berdampak langsung pada kualitas komponen, efisiensi biaya, dan kelancaran rantai pasok. Berikut adalah beberapa kriteria penting yang perlu dipertimbangkan:
- Kemampuan Teknis dan Teknologi:Evaluasi jenis dan kondisi mesin cutting yang dimiliki oleh distributor. Apakah mereka memiliki teknologi yang sesuai dengan kebutuhan spesifik pabrik otomotif, seperti mesin laser cutting (2D atau 3D), plasma cutting definisi tinggi, atau waterjet? Penting juga untuk mengetahui kemampuan mereka dalam memproses material spesifik, terutama Advanced High-Strength Steels (AHSS) dan grade baja otomotif lainnya, serta toleransi dimensi yang dapat mereka capai secara konsisten.
- Kualitas Material dan Sertifikasi:Pastikan distributor memiliki sumber pasokan material yang terpercaya dan dapat menyediakan sertifikasi material (mill certificate) yang menjamin komposisi kimia, sifat mekanik, dan traceability material. Sistem manajemen kualitas yang diterapkan oleh distributor, seperti sertifikasi ISO 9001 atau standar kualitas spesifik otomotif (misalnya, IATF 16949 jika relevan untuk layanan mereka), juga menjadi indikator penting.
- Kapasitas Produksi dan Waktu Pengerjaan (Lead Time):Distributor harus memiliki kapasitas produksi yang memadai untuk menangani volume pesanan dari pabrik otomotif, baik untuk pesanan reguler maupun fluktuasi permintaan. Kemampuan untuk memenuhi tenggat waktu pengiriman (lead time) yang disepakati sangat krusial untuk menjaga kelancaran lini produksi otomotif.
- Layanan Nilai Tambah Lainnya:Selain jasa cutting primer, pertimbangkan layanan nilai tambah lain yang ditawarkan, seperti kemampuan slitting (pembelahan koil), shearing (pemotongan lembaran), blanking (pembuatan potongan awal), manajemen inventaris (termasuk consignment stock atau Just-in-Time delivery), serta layanan fabrikasi ringan lainnya yang mungkin dibutuhkan.
- Reputasi dan Pengalaman:Cari tahu rekam jejak distributor dalam melayani industri otomotif atau industri lain yang memiliki standar kualitas dan ketepatan waktu yang tinggi. Testimoni dari pelanggan lain atau studi kasus bisa menjadi referensi yang berharga.
- Lokasi dan Kemampuan Logistik:Kedekatan geografis antara fasilitas distributor dan pabrik otomotif dapat memberikan keuntungan dalam hal efisiensi logistik, pengurangan biaya transportasi, dan waktu respons yang lebih cepat. Namun, kemampuan logistik distributor yang handal juga dapat mengkompensasi jarak yang lebih jauh.
- Harga yang Kompetitif dan Transparan:Meskipun kualitas dan layanan adalah prioritas, harga tetap menjadi faktor penting. Cari distributor yang menawarkan struktur harga yang kompetitif dan transparan, dengan keseimbangan yang baik antara kualitas produk, layanan yang diberikan, dan biaya keseluruhan.
Proses pemilihan distributor sebaiknya tidak hanya didasarkan pada penawaran harga termurah. Industri otomotif memerlukan mitra rantai pasok yang dapat diandalkan, memahami kebutuhan teknis yang unik, dan mampu berkontribusi secara proaktif terhadap efisiensi dan kualitas produksi secara keseluruhan. Ini adalah investasi dalam kemitraan jangka panjang yang solid.
Masa Depan Teknologi Cutting Besi di Industri Otomotif Indonesia: Menyongsong Era Industri 4.0 (Tren 2025 dan Seterusnya)
Industri otomotif Indonesia, seperti halnya di seluruh dunia, sedang bergerak menuju era Industri 4.0. Transformasi digital ini membawa implikasi signifikan bagi seluruh rantai nilai, termasuk teknologi dan proses cutting besi. Masa depan menjanjikan sistem yang lebih cerdas, terhubung, dan otomatis, yang akan merevolusi cara komponen otomotif diproduksi.
Adopsi Smart Technology dan Otomatisasi Penuh dalam Proses Cutting Besi
Tren global menunjukkan pergeseran menuju smart factory, di mana teknologi cutting besi tidak lagi berdiri sendiri, melainkan terintegrasi dalam ekosistem produksi yang cerdas. Di Indonesia, diperkirakan bahwa smart cutting tools dan solusi otomatisasi akan mencakup sekitar 19% dari pasar alat potong pada tahun 2030. Beberapa aspek kunci dari tren ini meliputi:
- Integrasi Sensor, IoT, dan AI: Mesin-mesin cutting modern akan semakin banyak dilengkapi dengan sensor-sensor canggih yang memantau berbagai parameter proses secara real-time (suhu, getaran, keausan alat, kualitas potongan). Data dari sensor ini, melalui konektivitas Internet of Things (IoT), akan dianalisis oleh algoritma Kecerdasan Buatan (AI) dan machine learning. Hasil analisis ini dapat digunakan untuk penyesuaian parameter potong secara otomatis guna menjaga kualitas optimal, melakukan pemeliharaan prediktif (predictive maintenance) untuk mencegah kerusakan mesin yang tidak terduga, dan mengoptimalkan penggunaan energi serta consumables.
- Robotika Lanjut: Penggunaan robotika akan melampaui sekadar tugas repetitif. Robot akan digunakan untuk loading/unloading material ke mesin cutting secara otomatis, penanganan komponen hasil cutting, dan bahkan melakukan beberapa jenis operasi cutting itu sendiri, terutama dalam sel kerja yang terintegrasi.
- Sistem Visi Komputer (Computer Vision): Teknologi visi komputer akan memainkan peran penting dalam inspeksi kualitas potongan secara otomatis dan real-time. Sistem ini dapat mendeteksi cacat minor, mengukur dimensi dengan presisi tinggi, dan memastikan setiap komponen memenuhi standar kualitas sebelum melanjutkan ke tahap produksi berikutnya, mengurangi kebutuhan inspeksi manual yang memakan waktu.
Masa depan cutting besi di industri otomotif tidak hanya tentang mesin yang lebih cepat atau lebih presisi secara individual, tetapi tentang penciptaan sistem produksi yang lebih cerdas, adaptif, dan terhubung. Sistem ini akan mampu belajar dari data, mengoptimalkan dirinya sendiri, dan meminimalkan intervensi manusia yang tidak perlu, sehingga meningkatkan efisiensi, konsistensi, dan fleksibilitas produksi secara keseluruhan.
Peran Industri 4.0 dalam Mengoptimalkan Rantai Pasok Layanan Cutting Besi Otomotif
Prinsip-prinsip Industri 4.0 tidak hanya berlaku di dalam pabrik, tetapi juga akan mentransformasi seluruh rantai pasok layanan cutting besi di sektor otomotif. Konektivitas dan pertukaran data akan menjadi kunci:
- Konektivitas Digital Antar Pemangku Kepentingan: Akan ada peningkatan konektivitas digital antara pabrik otomotif (OEM), distributor atau steel service center, dan bahkan produsen baja. Platform digital terintegrasi akan memfasilitasi komunikasi dan kolaborasi yang lebih lancar.
- Perencanaan Produksi dan Manajemen Inventaris Berbasis Data: Dengan berbagi data permintaan dan kapasitas produksi secara real-time, perencanaan produksi dapat dilakukan secara lebih akurat dan kolaboratif. Ini akan mengarah pada manajemen inventaris yang lebih efisien di seluruh rantai pasok, mengurangi lead time, dan meningkatkan responsivitas terhadap perubahan permintaan pasar.
- Penggunaan Digital Twins: Teknologi digital twin (replika digital dari aset fisik atau proses) akan memungkinkan simulasi proses cutting dan optimasi parameter sebelum produksi fisik dimulai. Ini dapat membantu mengidentifikasi potensi masalah, mengurangi limbah material selama uji coba, dan mempercepat waktu pengembangan produk baru.
- Peningkatan Traceability Material dan Komponen: Dengan sistem digital yang terintegrasi, pelacakan material dari sumbernya hingga menjadi komponen jadi akan menjadi lebih mudah dan akurat. Ini penting untuk kontrol kualitas, pemenuhan regulasi, dan penanganan isu recall jika terjadi.
Kementerian Perindustrian Republik Indonesia telah menunjukkan komitmen untuk mendukung implementasi teknologi canggih seperti AI, machine learning, dan digitalisasi di semua sektor industri, sejalan dengan peta jalan Making Indonesia 4.0. Industri 4.0 akan mengubah cara layanan cutting besi direncanakan, dieksekusi, dan dikelola dalam ekosistem otomotif. Ini akan menciptakan rantai pasok yang lebih transparan, responsif, kolaboratif, dan efisien, di mana pabrik otomotif dan mitra distributor mereka dapat beroperasi sebagai satu kesatuan yang terintegrasi secara digital, mengoptimalkan aliran material dan informasi dari hulu ke hilir.
Tantangan dan Peluang bagi Industri Otomotif dan Distributor Besi Baja Indonesia
Transisi menuju teknologi cutting besi yang lebih canggih dan terintegrasi dalam kerangka Industri 4.0 menghadirkan serangkaian tantangan dan peluang bagi industri otomotif serta distributor besi baja di Indonesia.
Tantangan yang Perlu Diatasi:
- Investasi Awal Teknologi Tinggi: Adopsi mesin cutting modern, robotika, dan sistem perangkat lunak cerdas memerlukan investasi awal yang signifikan. Ini bisa menjadi kendala, terutama bagi pemain skala kecil dan menengah.
- Kebutuhan Sumber Daya Manusia (SDM) Terampil: Mengoperasikan dan memelihara teknologi canggih memerlukan SDM dengan keahlian baru di bidang otomasi, analisis data, dan pemrograman. Pengembangan talenta menjadi krusial.
- Standarisasi Data dan Interoperabilitas Sistem: Untuk mencapai konektivitas rantai pasok yang sesungguhnya, diperlukan standarisasi format data dan kemampuan sistem yang berbeda untuk saling berkomunikasi (interoperability).
- Keamanan Siber: Dengan semakin terhubungnya sistem produksi, risiko serangan siber dan kebocoran data sensitif juga meningkat, memerlukan langkah-langkah keamanan yang kuat.
- Fluktuasi Harga Bahan Baku: Volatilitas harga baja global tetap menjadi tantangan bagi perencanaan biaya produksi.
- Kebutuhan Inovasi Berkelanjutan: Teknologi berkembang pesat, menuntut perusahaan untuk terus berinovasi agar tidak tertinggal.
Peluang yang Dapat Diraih:
- Peningkatan Produktivitas dan Efisiensi: Otomatisasi dan optimasi proses melalui teknologi cerdas dapat secara dramatis meningkatkan produktivitas, mengurangi waktu siklus, dan menekan biaya operasional jangka panjang.
- Peningkatan Kualitas dan Konsistensi Produk: Proses cutting yang lebih presisi dan terkontrol akan menghasilkan komponen dengan kualitas yang lebih tinggi dan konsisten, mengurangi tingkat cacat dan rework.
- Peningkatan Daya Saing Global: Dengan mengadopsi teknologi manufaktur canggih, industri otomotif Indonesia dapat meningkatkan daya saingnya di pasar global, baik untuk pasar domestik maupun ekspor.
- Pengembangan Produk Inovatif: Kemampuan untuk memproses material canggih seperti AHSS dengan presisi tinggi membuka peluang untuk desain kendaraan yang lebih inovatif, termasuk untuk kendaraan listrik (EV) yang memerlukan struktur ringan namun kuat.
- Dukungan Pemerintah: Pemerintah Indonesia telah menunjukkan komitmen untuk mendorong industrialisasi dan adopsi teknologi melalui berbagai inisiatif dan insentif, yang dapat membantu meringankan beban investasi dan memfasilitasi transisi.
- Pertumbuhan Pasar Otomotif: Pasar otomotif domestik Indonesia yang besar dan potensi pertumbuhan ekspor memberikan landasan permintaan yang kuat untuk komponen berkualitas tinggi.
- Pengembangan Ekosistem Lokal: Tantangan ini juga membuka peluang bagi pengembangan ekosistem pendukung lokal, termasuk penyedia solusi teknologi, lembaga pelatihan kejuruan, dan pusat riset yang fokus pada manufaktur canggih. Peran industri baja nasional dalam memasok bahan baku berkualitas juga menjadi sangat penting.
Transisi ke teknologi cutting besi yang lebih maju dan terintegrasi dalam paradigma Industri 4.0 adalah sebuah keniscayaan bagi industri otomotif Indonesia jika ingin terus bertumbuh dan bersaing secara global. Ini memerlukan upaya kolaboratif yang melibatkan pemerintah, pelaku industri (baik OEM maupun distributor/pemasok), serta institusi pendidikan dan riset untuk membangun ekosistem yang kondusif, mengembangkan SDM yang kompeten, dan mendorong inovasi berkelanjutan.
Kesimpulan
Proses cutting besi telah terbukti sebagai elemen esensial yang mengalami evolusi signifikan dalam dinamika industri otomotif. Tuntutan akan presisi yang tak kenal kompromi, efisiensi produksi yang tinggi, serta kemampuan untuk menangani material-material canggih seperti Advanced High-Strength Steels (AHSS) telah mendorong inovasi berkelanjutan dalam teknologi pemotongan. Metode modern seperti laser cutting dan plasma cutting, yang didukung oleh otomatisasi tingkat lanjut dan sistem kontrol numerik (CNC), kini memainkan peran kunci dalam membentuk komponen-komponen kendaraan dengan akurasi dan kecepatan yang sebelumnya sulit dicapai. Lebih lanjut, sinergi strategis antara pabrik otomotif dan distributor besi baja yang tidak hanya memasok material tetapi juga menyediakan layanan cutting bernilai tambah, telah menjadi faktor krusial dalam mencapai keunggulan kompetitif di pasar yang semakin ketat.
Keberhasilan manufaktur otomotif modern, dari tahap desain hingga produk akhir yang meluncur di jalan, sangat bergantung pada penguasaan dan penerapan teknologi cutting besi yang tepat dan optimal. Ini bukan lagi sekadar operasi pendukung, melainkan bagian integral dari strategi produksi yang menentukan kualitas, biaya, dan kecepatan respons terhadap pasar.
Di tengah persaingan global yang kian intensif dan tuntutan inovasi yang tak pernah berhenti, investasi berkelanjutan dalam teknologi cutting besi termutakhir serta pengembangan kemitraan strategis yang solid dalam seluruh rantai pasok akan menjadi pilar utama bagi pertumbuhan dan keberlanjutan industri otomotif. Hal ini menjadi semakin relevan bagi Indonesia, yang tengah berupaya mengakselerasi transformasi menuju era Industri 4.0, di mana efisiensi, presisi, dan konektivitas menjadi kata kunci. Dengan memanfaatkan teknologi cutting terkini dan memperkuat kolaborasi antara semua pemangku kepentingan, industri otomotif nasional memiliki potensi besar untuk terus berkembang dan memberikan kontribusi signifikan bagi perekonomian.